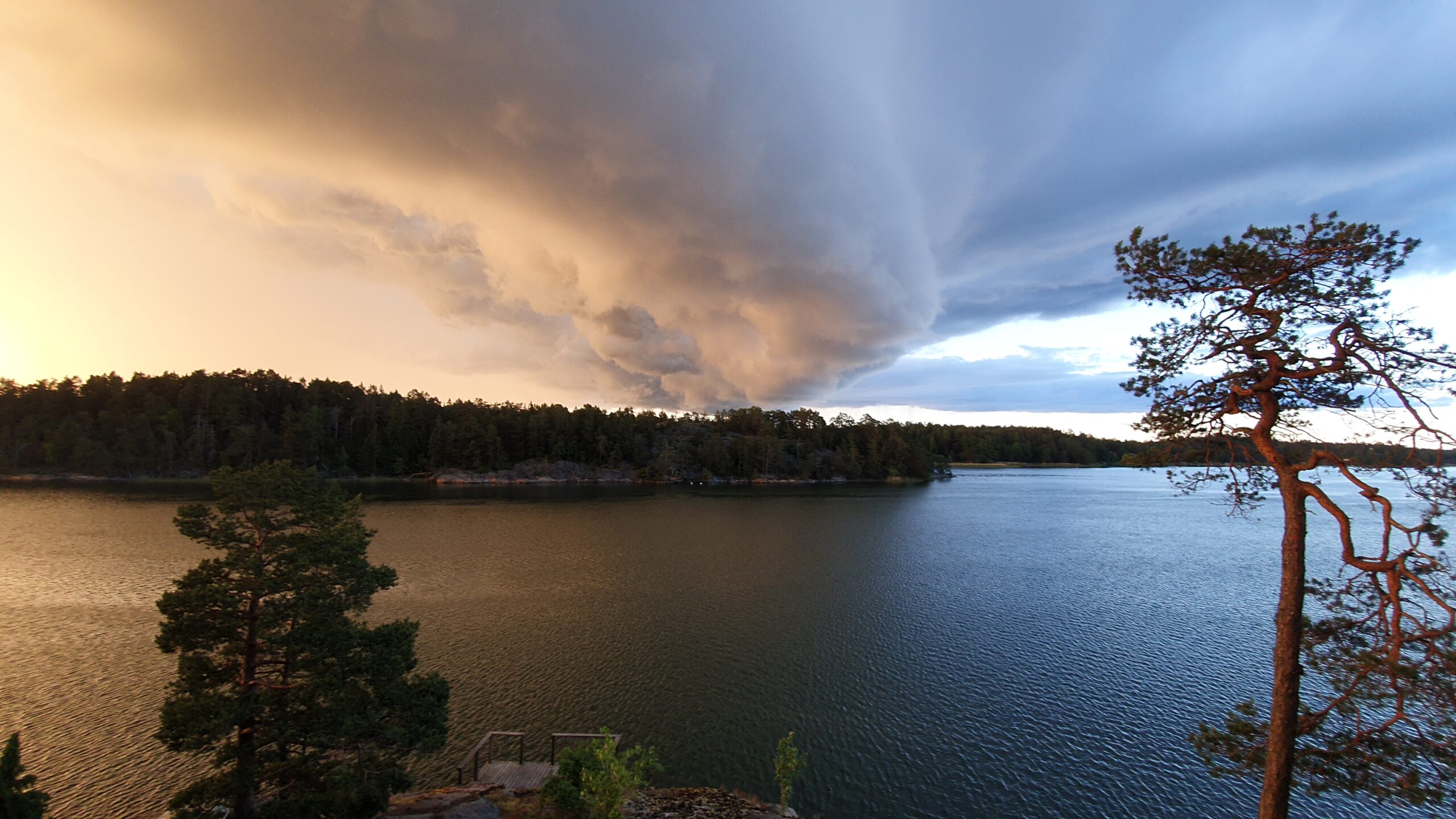
We enable energy-efficient emission-free steel
for a world without fossil emissions
Production of
50 thousand – 3 million
annual tonnes of steel
from
FerroSilva DRI…
requires
0.015-0.9
TWh electricity/year
about
90%
lower than hydrogen alternatives…
and
0.18–10.5
TWh biomass/year
which is
0.3-19%
of unutilised biomass in Sweden
We are revolutionising the steel industry
The resulting CO2 reduction of
150 thousand – 9 million tonnes/year compared to blast furnace production…
corresponds to
emissions from
1 250 million – 62 500 million kilometres of driving a
petrol car…
or
125 thousand – 6.25 million petrol cars driving
10 000 kilometres per year
FerroSilva’s sponge iron production method generates a carbon sink of 845 kg of CO2 per tonne of steel if the biogenic carbon dioxide is recovered and turned into new products or e-fuel.
This is a difference from today’s ore-based production with blast furnaces of about three tonnes of carbon dioxide per tonne of steel.
Production of 50 thousand tonnes of sponge iron, which is planned in FerroSilva’s first plant, corresponds to a reduction in emissions of almost 150 thousand tonnes of carbon dioxide.
This in turn corresponds to more than 1 250 million kilometres travelled by a petrol car emitting 120g CO2/km
or more than 125 thousand passenger cars driving 10 000 kilometres per year.
If all of Sweden’s ore-based steel production from 3 million tonnes of blast furnace iron were replaced by the FerroSilva process, the savings would increase a further 50 times to 9 million tonnes of carbon dioxide corresponding to 62.5 million kilometres or 6.25 million cars.
Can this really be true?
We have collected questions and answers here.
Biomass to make reducing gas has a high added value
The FerroSilva process adds more value to biomass, by utilising its full chemical potential, than heat and electricity production.
This increases the value of this raw material and the possibilities to collect residues that are currently left to rot in the forest.
Established process technology makes the FerroSilva process resource efficient
By combining established industrial processes in a new way, the prerequisites are created for solving the need for pure iron raw material in a way that Sweden’s electricity grid and the availability of biomass can handle.
Biogenic carbon dioxide and CCU provide a carbon sink
In a calculation for 1 tonne of crude steel, a growing forest absorbs 1 205 kg carbon dioxide.
The process steps leading up to steel emit some 360 kg, but if the carbon dioxide collected from the FerroSilva process is used for products (CCU), a carbon sink of 845 kg of carbon dioxide per tonne of steel is created.
The FerroSilva process is cost-competitive
A cost comparison carried out where production with natural gas + CCS (brown), biogenic syngas with CCU (green) and hydrogen from electrolyser (blue) are compared under otherwise identical conditions, showed that the FerroSilva process is competitive at medium natural gas prices and normal electricity prices.
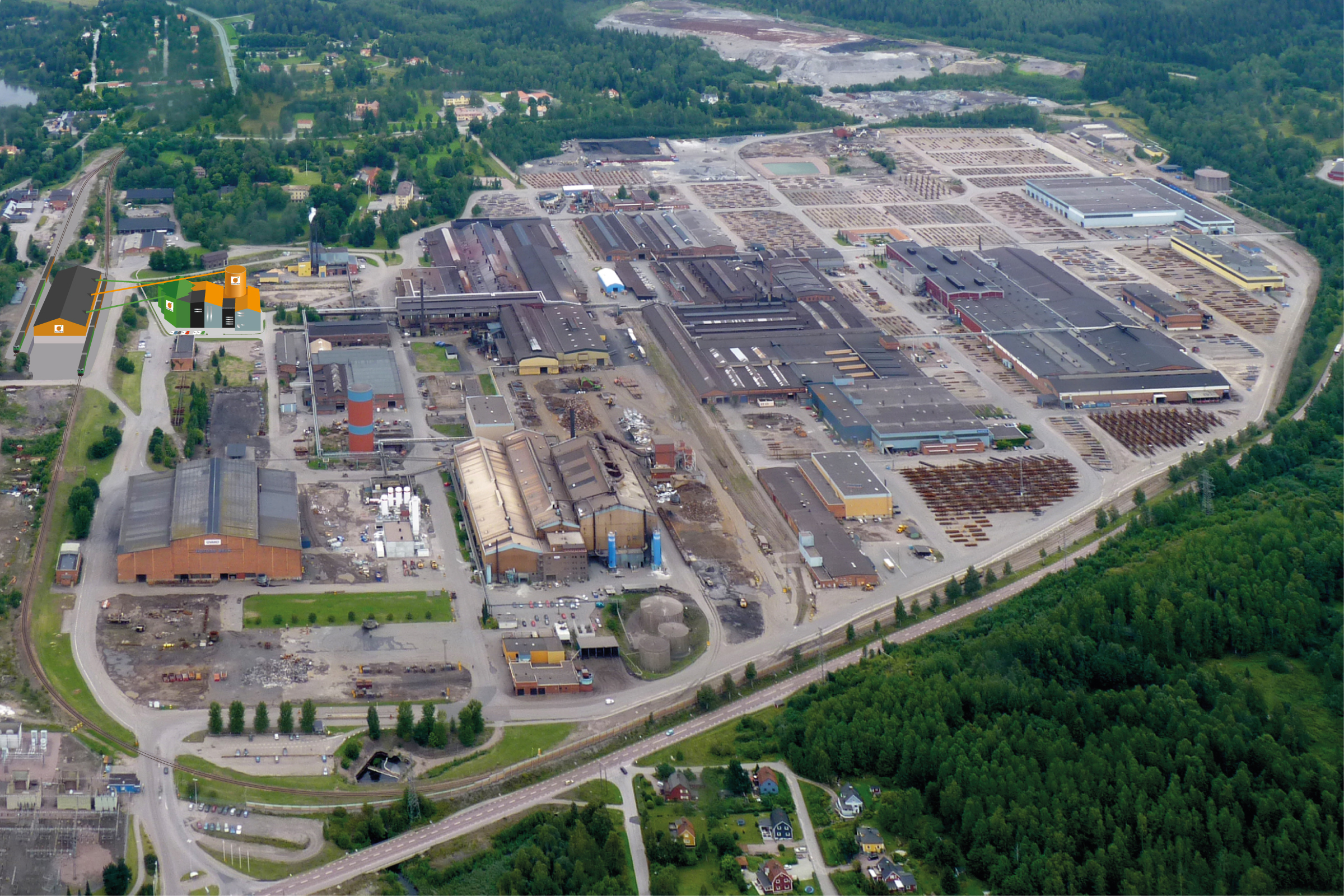
We are now working on a first plant
of 50,000 tonnes per year of DRI
We are targeting Ovako’s HOFORS site
Now it’s time to get started.
FerroSilva’s management is today a team with decades of experience in leading positions in the Swedish and European steel industry, research and finance.
“Together we have started FerroSilva to revolutionise the steel industry and reduce global climate emissions, something we are all passionate about.”
We will tell you more about this when we are further along.